THE ONGOING GLOBAL CHIP SHORTAGE: PARALYZING AND HALTING PRODUCTION
- 180DC SGGSCC
- Jan 20, 2022
- 3 min read
A storm of adverse events and increased demand has led to a big crisis which essentially involves tiny components, i.e., “The Semiconductor Microchips”, often referred to as the brains of modern electronics.
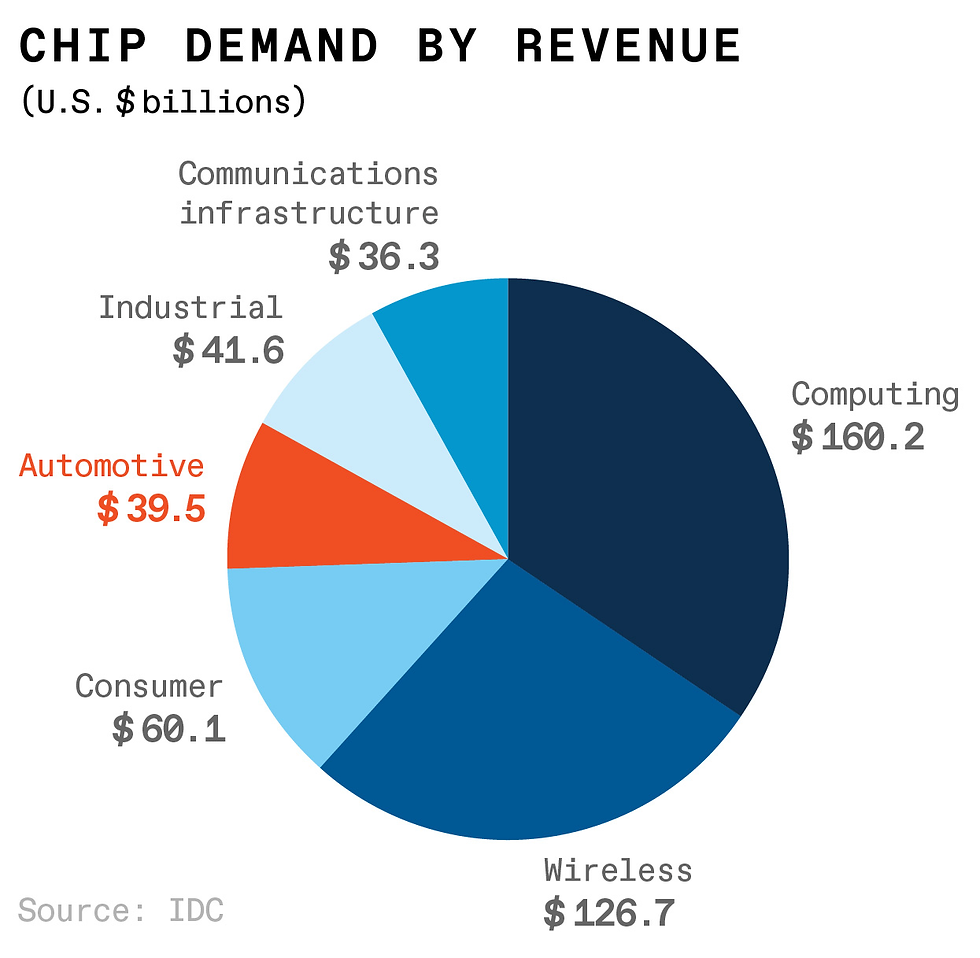
The global shortage of semiconductors has created serious anxiety in a significant number of industries and even caused automakers to halt production in several factories worldwide.
As a consequence of the pandemic, several factories have been forced to shut down in order to abide by government regulations, facilitating a huge shortfall in the availability of supplies to manufacture these chips. Moreover, with work from home, the demand for consumer electronics has steadily increased, causing a huge gap in the demand and supply of these chips.
To add to the problem, the on-going crisis has also forced China to close-down the Yantian Port, the supply route for a whopping 90% of the world’s electronics to pass through. This has subsequently obligated many container ships to wait for docking, thereby increasing the lead times for chip delivery.


The shortage of these semiconductor chips, which are often referred to as the “heart” of billions of products (ranging from smartphones, data centers, computers, laptops, tablets, smart devices, vehicles, household appliances, life-saving pharmaceutical devices, agri-tech, ATMs and more) has forced the makers to increase the prices due to the increase in the input cost and the cost related to production, extracting an inflated price from the consumer.
In India, Maruti Suzuki hiked car prices recently due to the increased cost of production. Taiwan Semiconductor Manufacturing Company reporting a profit increase of 11% from the previous year, alongside a revenue growth of 28% is a testimonial to this fact. By 2022, TSMC is also expected to raise the prices of its chips by as much as 20%, which could have a knock-on effect of raising prices for consumer electronics by 2022.
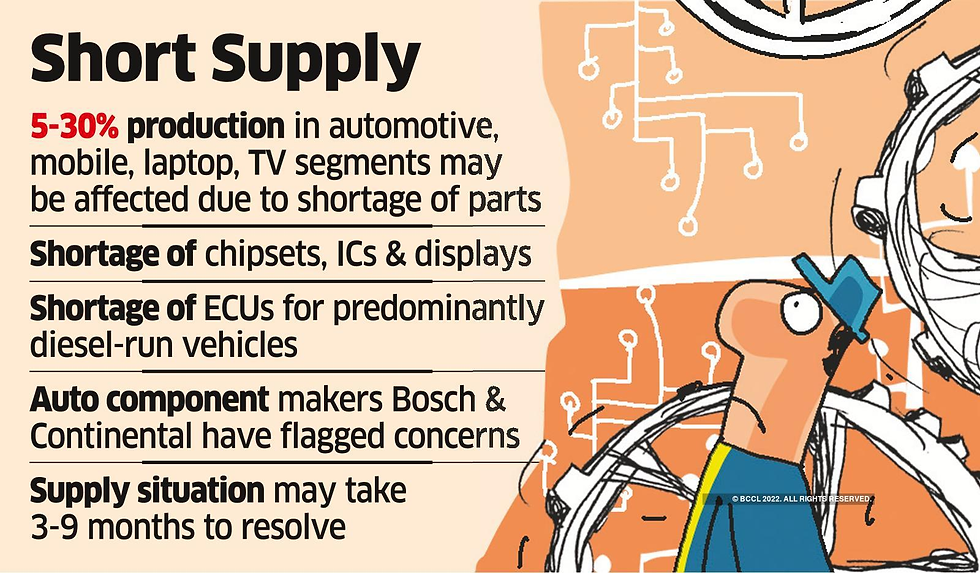
To deal with this crisis, the makers who had a previous stock of chips in their inventory were using it for manufacturing of new products towards the beginning of this crisis. However, currently, despite ongoing efforts to shore up the supply chain, semiconductor availability has worsened as the makers exhaust stockpiles and other industries have no more to spare. This can even lead to a monopoly in the acquisition of chips by the big market players of the industries. Companies are trying to stockpile chips to last them through the crisis. But hoarding will further distort the demand signals that are rippling through the supply chain, making it seem like companies need far more chips than are actually needed to meet consumer demand and the other companies will not be able to acquire them at the same time due to limited production either.

In the midst of this, India has the potential to become the next electronic chip hub.
Smartphone assembly units have expanded from 2 in 2014 to 200 in 2021 owing to Make in India and government efforts, making India the world's largest mobile manufacturer. This has now created sufficient domestic demand to justify semiconductor production in India and to a great extent, has created the requisite infrastructure and know-how.
While chip shortages are likely to remain in the coming months, plans for supply resiliency are being crafted. In response to this, India, Japan, and Australia formally launched the Supply Chain Resilience Initiative (SCRI). The countries will share best practices on supply chain resilience as part of the SCRI, as well as host investment promotion and buyer-seller matching events to allow stakeholders to diversify their supply chains.

TSMC, which is responsible for producing about 80% of microcontroller chips used in cards, said that it would invest 2.87 billion US Dollars to expand mature capacity in Nanjing, China.
According to Pat Gelsinger, CEO, Intel Corp, plans on allocating some of the capacity to cars, a market which has not previously been focused on by them are being devised. Nividia, on the other hand has addressed the shortfall in the Graphic Processing Units by bringing back older versions, which are based on older process nodes which will essentially not have to compete for leading-edge capacity at the foundries.
Furthermore, companies may be forced to reassess, at least in part, their existing practices of just-in-time delivery and low stock levels throughout their value chains. While India has made great progress in electronic component manufacture and chip design, it still has a long way to go before it can be considered a semiconductor manufacturing hub. There are intrinsic limitations that need to be overcome and challenges that need to be tackled head-on with a concrete strategy, critical support, concerted action and realistic, forward-looking policies.
Interesting